Dealing with a malfunctioning icemaker can be a real hassle. Are you tired of constantly troubleshooting your icemaker issues? Wondering how to navigate the do’s and don’ts of this frustrating situation? In this guide, we’ll provide you with practical tips to handle your malfunctioning icemaker like a pro. From simple troubleshooting steps to common pitfalls to avoid, we’ve got you covered. Stay tuned to learn how to tackle icemaker problems effectively and efficiently.
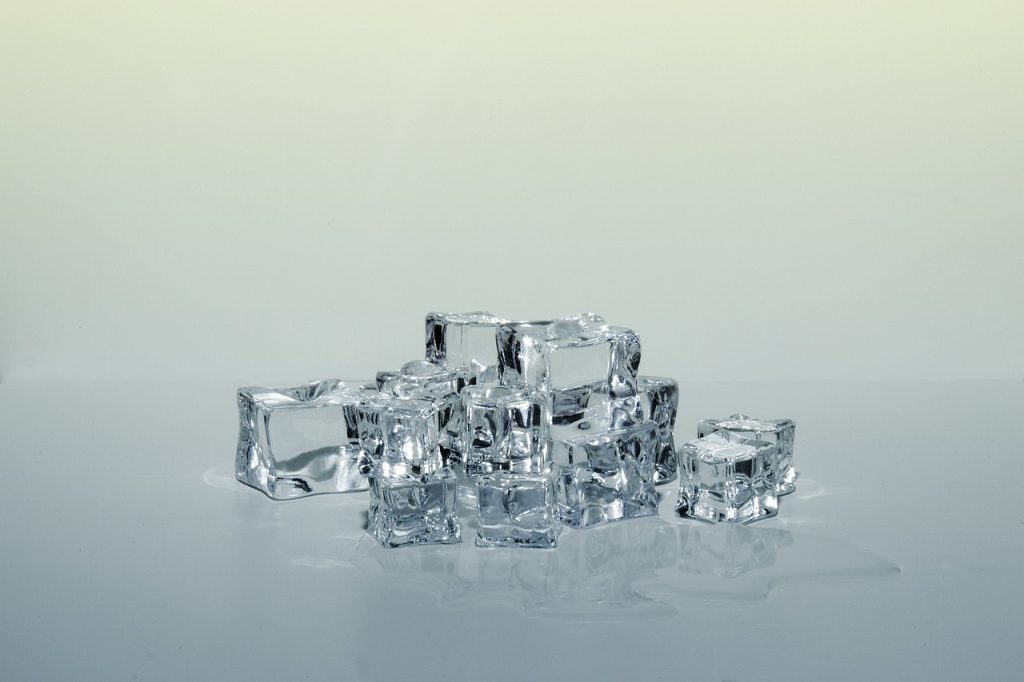
Common Ice Maker Problems
Ice Not Being Made
- Verify the control arm is functioning correctly and not stuck in the off position.
- Ensure the freezer temperature is set to around 0°F for optimal ice production.
- Check for any kinks or twists in the water line that may restrict water flow.
Ice Not Dispensing
- Inspect the ice bin placement to ensure it is properly aligned with the dispensing mechanism.
- Clear any ice clumps that may be blocking the dispensing chute.
- Test the control arm to confirm it is not preventing ice from being dispensed.
Ice Maker Freezing Inside
- Defrost the water inlet tube if it appears frozen to restore proper function.
- Adjust temperature settings to prevent excessive freezing within the ice maker.
- Regularly check for mineral deposits on freezing rods that could cause freezing issues.
Odd-Shaped Ice Production
- Examine the water supply for any irregularities that might affect ice shape.
- Check the ice mold for damage or misalignment that could lead to odd shapes.
- Ensure the ice maker is level to promote even ice formation.
Troubleshooting Steps
Check Water Supply
- Confirm the water supply line is securely connected to the ice maker.
- Inspect for leaks, blockages, or ice makers that could hinder water flow.
- Test water pressure to meet the ice maker’s requirements.
Inspect For Blockages
- Look for ice clumps obstructing normal operation.
- Clear debris around the water inlet and ice mold.
- Ensure the ice bin is not overfilled, preventing blockages.
Examine Temperature Settings
- Verify appropriate temperature settings for ice production.
- Adjust settings if producing insufficient or excessive ice.
- Monitor internal temperature regularly for optimal conditions.
Reset The Ice Maker
- Follow the manufacturer’s instructions to perform a reset.
- Disconnect power briefly before reconnecting to reset functions.
- Observe if resetting resolves ongoing issues with ice production.
Do’s Of Handling Issues
Follow Safety Precautions
Always unplug the ice maker before starting any maintenance or repairs to avoid electrical hazards. Wear protective gear such as gloves and safety goggles when handling sharp components or tools to prevent injuries. Ensure the area around the ice maker is clear to prevent accidents and provide ample space to work safely.
Refer To User Manual
Consult the user manual provided by the manufacturer for specific troubleshooting steps tailored to your ice maker model. Adhere to the guidelines outlined in the manual for maintenance and care practices that can extend the lifespan of your appliance. Utilize the manual as a valuable reference for understanding the various features and settings of your ice maker.
Use Recommended Tools
Use only manufacturer-recommended tools when performing repairs on your ice maker to ensure precision and prevent damage. Keep essential tools like screwdrivers and pliers readily available for quick fixes or routine maintenance tasks. Avoid using makeshift tools that may not be suitable for the job, as they could potentially harm the integrity of your ice maker.
Test After Each Fix
After making any adjustments or repairs, always conduct a test cycle on your ice maker to confirm that the issue has been resolved successfully. Monitor the performance of the ice maker closely following each fix to ensure that it is functioning as expected. Document any changes in functionality to keep track of the progress made in resolving the issue.
Don’t Of Repairing Ice Makers
Avoid Forcing Components
Handle all parts gently to prevent breakage or misalignment. Respect the design by avoiding unnecessary manipulation when removing ice clumps or adjusting components.
Do not use excessive force, as it can damage the delicate mechanisms within the ice maker.
Do Not Ignore Leaks
Address any leaks immediately to prevent water damage and further issues. Inspect connections and seals for wear or damage signs. Regularly monitor the ice maker for leaking water.
- Ignoring leaks can lead to more significant problems like mold growth or electrical malfunctions.
Avoid Overloading The Unit
Limit the amount of ice stored in the bin to prevent mechanical strain. Regularly empty the ice bin for optimal ice production levels. Ensure proper airflow and function by providing enough space around the ice maker.
- Overloading the unit can lead to decreased efficiency and potential breakdowns.
Do Not Use Unapproved Parts
Only replace parts recommended by the manufacturer to ensure compatibility and functionality. Avoid generic parts that may not fit or work correctly in your ice maker.
- Using unapproved parts can void warranties and cause further damage to the appliance.
When To Seek Help
Recognize Persistent Problems
Persistent issues with your icemaker can be a sign of underlying mechanical problems. Document these recurring issues to share with professionals if necessary. Addressing them promptly can prevent expensive repairs.
Identify Electrical Issues
Examine for blown fuses or tripped circuit breakers that may be affecting your icemaker’s operation. Inspect the power cord for any damage or loose connections. Test the outlet using another appliance to ensure a consistent power supply.
Know When To Call Experts
For intricate problems that go beyond basic troubleshooting, it’s advisable to seek help from professionals. Look out for signs of significant malfunction that require expert intervention. If you’re uncertain about repairs or maintenance, consulting a technician is recommended.
Understand Warranty Terms
Understanding your warranty coverage is crucial to determining which repairs are covered. Maintain records of purchases and repairs for potential warranty claims in the future. Keep track of warranty expiry dates to make the most of the coverage provided.
Preventive Maintenance Tips
Regular Cleaning Routine
Establish a cleaning schedule to maintain hygiene and performance. Consistently cleaning the icemaker prevents mold and bacteria buildup, ensuring clean ice production. Use approved cleaning solutions to avoid damaging components. Harsh chemicals can harm the icemaker’s internal parts, affecting its functionality. Pay special attention to the ice bin and water lines during cleaning. These areas are prone to debris accumulation, impacting ice quality.
Inspect Water Lines
Regularly check water lines for signs of wear, leaks, or blockages. Damaged or clogged water lines can lead to reduced ice production or even complete malfunction. Ensure connections are tight and secure to prevent water loss. Loose fittings can cause leaks, affecting the icemaker’s efficiency. Replace any damaged water lines promptly to maintain function. Timely replacement prevents further damage and ensures smooth operation.
Schedule Professional Checks
Plan regular maintenance checks with a qualified technician. Professional inspections help identify underlying issues early, preventing major breakdowns. Schedule inspections at least once a year to catch potential issues early. Regular professional checks prolong the lifespan of the icemaker and ensure optimal performance. Use professional services for thorough cleaning and servicing. Experts have the knowledge and tools to perform comprehensive maintenance, extending the icemaker’s longevity.
Adjust Temperature Settings
Fine-tune temperature settings based on seasonal changes and usage. Optimal temperature settings maximize ice production and quality throughout the year. Monitor ice production and adjust settings accordingly for optimal results. Regular monitoring helps maintain consistent ice output for your needs. Keep track of temperature fluctuations that may affect performance. Sudden temperature changes can impact ice formation, requiring adjustments for efficient operation.
Summary
In dealing with a malfunctioning icemaker, you have learned about common problems, troubleshooting steps, do’s and don’ts, when to seek help, and preventive maintenance tips. By following the advice provided, you can save time, money, and frustration. Remember to tackle issues promptly, avoid common pitfalls, and know when expert assistance is necessary. Regular maintenance will keep your icemaker running smoothly. Stay proactive in addressing any signs of trouble to prevent larger problems down the line.
Remember, taking care of your icemaker pays off in the long run. So, stay informed, be proactive, and enjoy hassle-free ice production. Your well-maintained icemaker will thank you with a constant supply of ice whenever you need it.
Frequently Asked Questions
1. How Can I Troubleshoot Common Issues With My Icemaker?
To troubleshoot common issues with your icemaker, check the water supply, temperature settings, and ice bin. Ensure the unit is level and free of debris. Refer to the manufacturer’s manual for specific troubleshooting steps.
2. What Are The Essential Do’s When Handling Icemaker Problems?
Do regularly clean the icemaker, inspect water supply lines for leaks, and replace filters as recommended. Keep the freezer temperature at the optimal level and follow the manufacturer’s maintenance guidelines.
3. What Are The Key Don’ts When It Comes To Repairing Ice Makers?
Don’t attempt to repair complex internal components if you lack experience. Avoid using sharp objects to break ice jams. Never ignore unusual sounds or leaks; seek professional help promptly.
4. When Should I Consider Seeking Professional Help For My Malfunctioning Icemaker?
Seek professional help if you notice persistent issues despite troubleshooting efforts, encounter electrical problems, or face challenges with internal components. Professional technicians have the expertise to diagnose and repair complex icemaker problems effectively.
5. What Preventive Maintenance Tips Can Help Extend The Lifespan Of My Icemaker?
Regularly clean the unit, inspect water lines for damage, replace filters on schedule, and ensure proper ventilation around the appliance. Monitor ice production patterns for any changes that could indicate underlying issues.
Zuta Appliance Repair: Expert Icemaker Malfunction Repair For Your Berkeley Kitchen
In the heart of Berkeley, California, Zuta Appliance Repair is your trusted partner for maintaining the functionality and convenience of your home. When your icemaker malfunctions, it can disrupt your kitchen’s efficiency, especially during those hot California days. That’s why we’re dedicated to providing top-tier icemaker repair services. Our expertise ensures your icemaker is back to producing ice efficiently, preventing any inconvenience and keeping your kitchen running smoothly. With Zuta Appliance Repair, you’re not just getting a repair—you’re receiving a commitment to quality, integrity, and reliability, enhancing both your kitchen’s performance and your peace of mind.
Experience comprehensive solutions to all your icemaker issues with Zuta Appliance Repair. Our specialized services are designed to extend the life of your appliance and restore your kitchen’s functionality. Our skilled team, equipped with unmatched expertise and a friendly approach, offers cost-effective solutions that ensure long-lasting results. This is more than just a repair service—it’s about restoring convenience and comfort to your home. Choose Zuta Appliance Repair for an improved lifestyle. Contact us now at (415) 592-4633 and let us get your icemaker back to being a reliable part of your daily life, offering cool convenience and peace of mind.
Disclaimer
The materials available on this website are for informational and entertainment purposes only and not to provide legal or professional advice. You should contact your attorney or home improvement specialist to obtain advice concerning any particular issue or problem. You should not act or refrain from acting based on any content included in this site without seeking legal or other professional advice. The information presented on this website may not reflect the most current home improvement developments. No action should be taken in reliance on the information on this website. We disclaim all liability concerning actions taken or not taken based on any or all of the contents of this site to the fullest extent permitted by law.